TFL Uses Custom Molding Techniques to Make Precast Refractory Shapes With Extremely Tight Tolerances
With Proper Attention to Dimensional Tolerances, Field Fit-up Problems With Precast Shapes Go Away
The manufacture of precast refractory shapes inherently requires the use of some type of mold or pattern to form the castable into the desired shape. Some precast applications may require extremely tight dimensional tolerances, while others require less. The level of dimensional tolerance required for a shape (“tight” or “loose”) is an important consideration when designing the mold and determining the type of mold materials to be used.
For simplistic shapes with relatively loose dimensional tolerances (281) 590-8500”), plywood or metal fabricated forms are commonly used. Styrofoam is also commonly used when dimensional tolerances are not so strict. On the other hand, shape applications with extremely tight dimensional tolerances (281) 590-8500” or less), may require the use of more sophisticated molds and materials.
Precast Shape
Applications
Requiring
Tight Dimensional Tolerances:
- Pipe inserts
- Kiln nose-rings
- Burner blocks (with precise ignitor or sensor locations)
- Shapes with preset anchoring locations
Precast Shape
Applications
Requiring
Less Stringent Dimensional Tolerances:
- Pier block s
- Furnace hearth blocks
- Support structures
- Manway openings
- Furnace doorway shapes
Depending on the requirements of a particular application , molds may also incorporate precisely machined, milled or sanded surfaces, similar to a metal-casting foundry pattern. No matter the application, TFL offers engineering services and field support to help you with the design of a successful precast shape system.
Contact us today to discuss your next precast project!
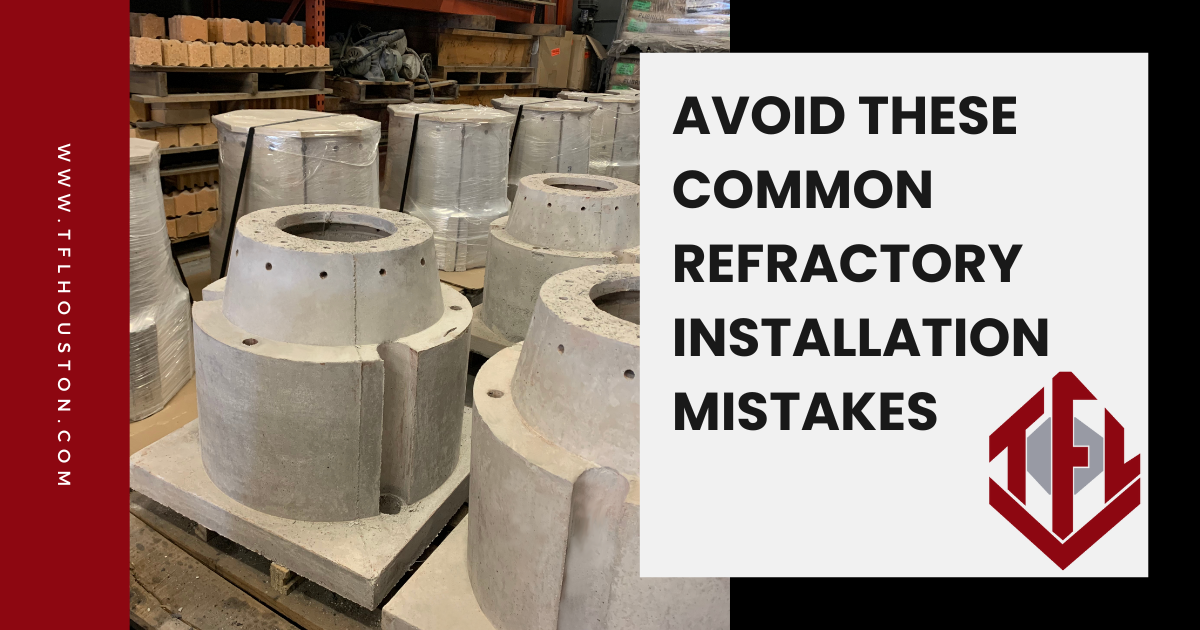
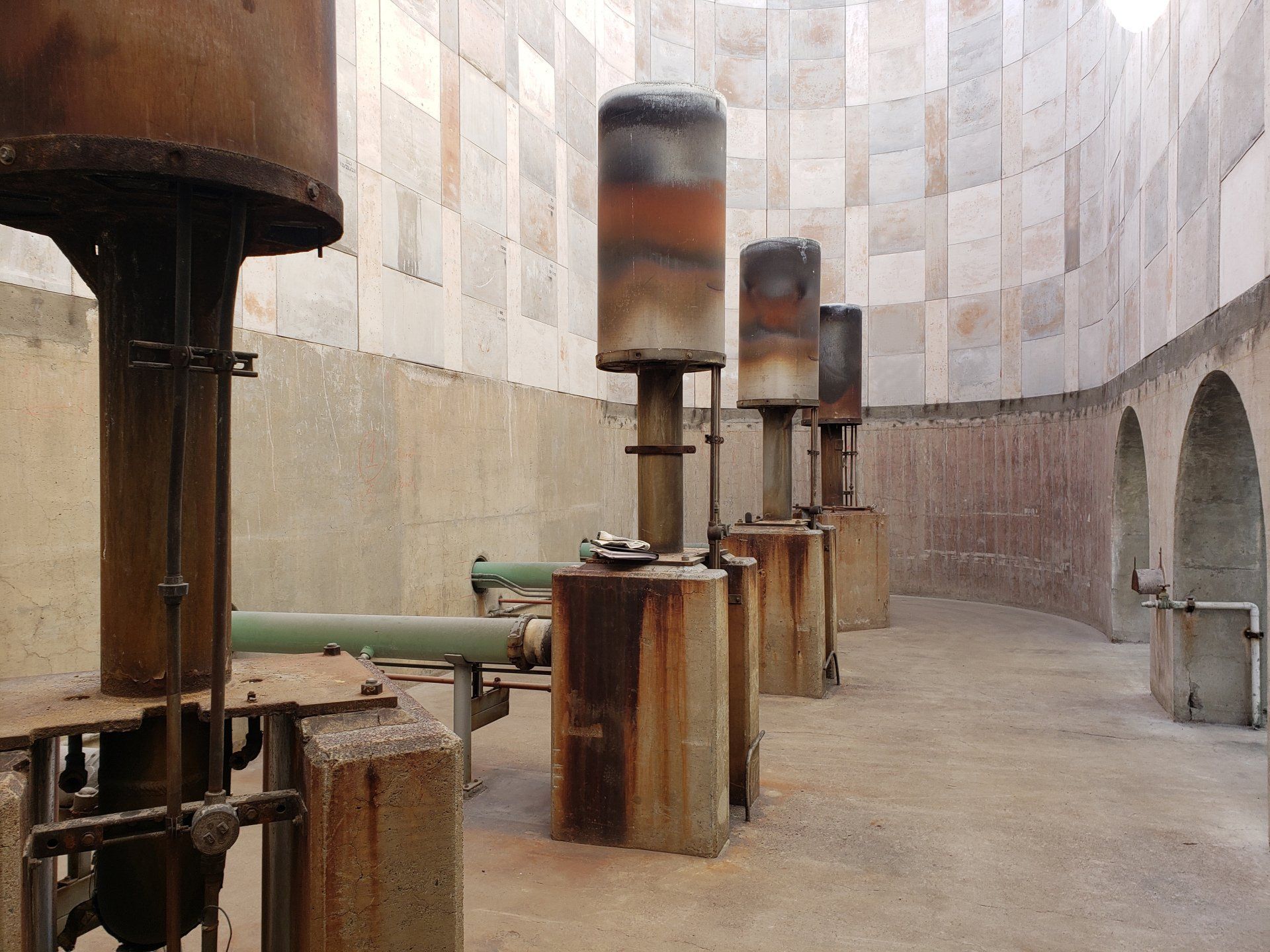
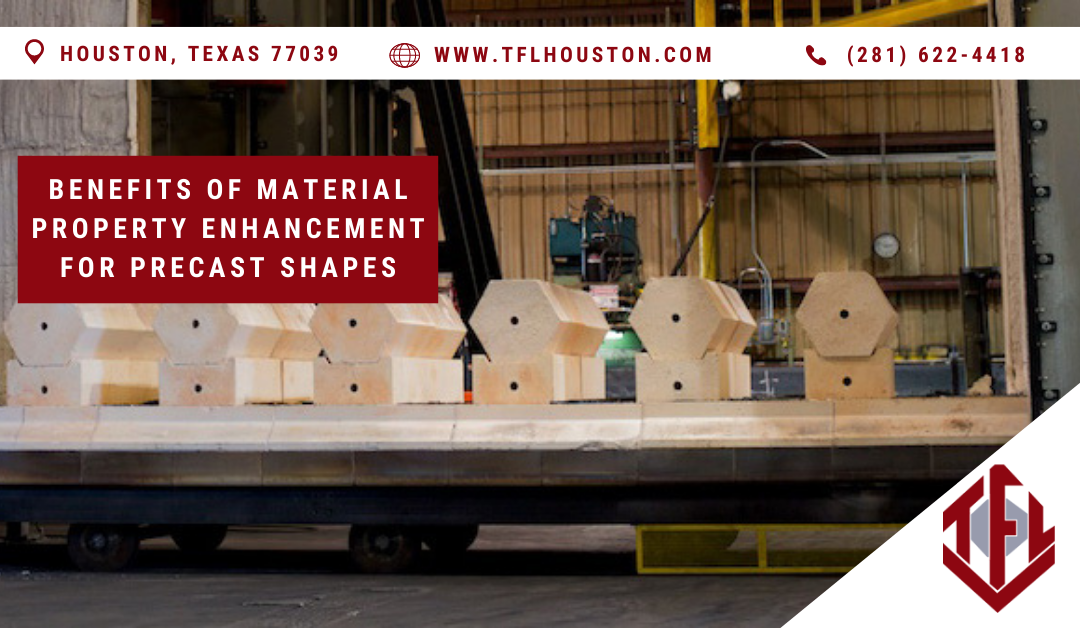
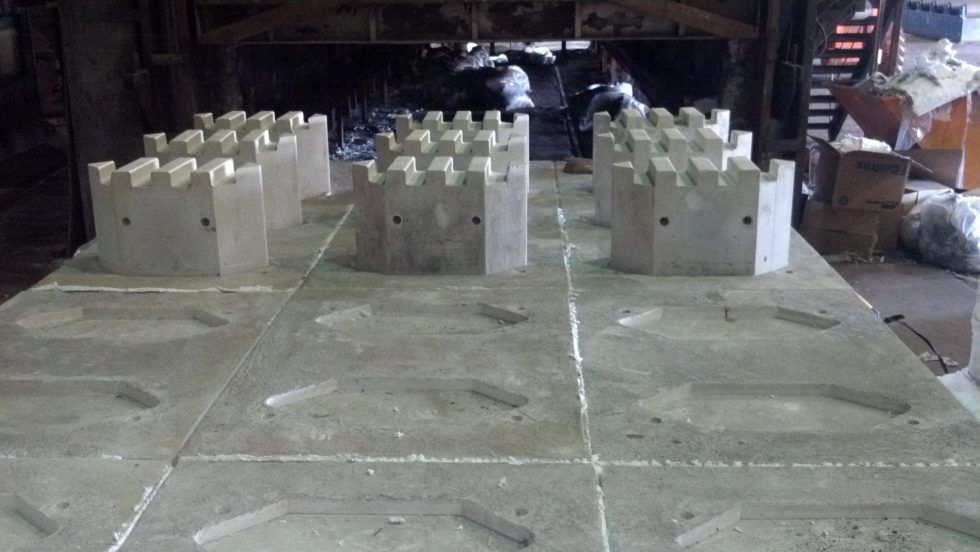
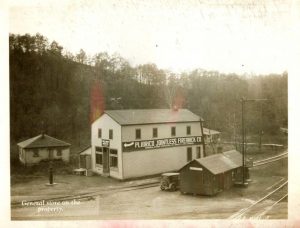
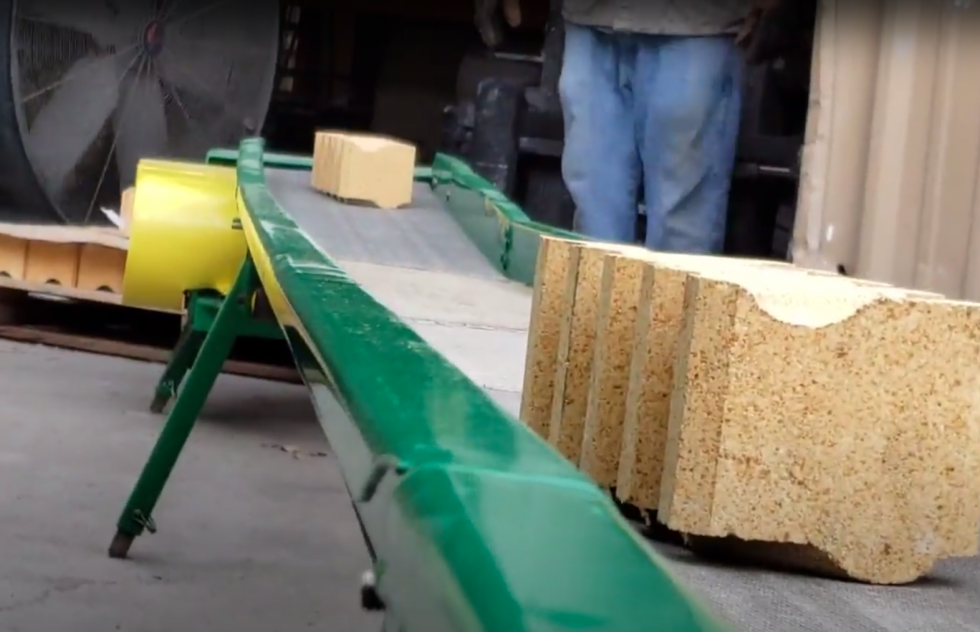