Why Refractories Fail & How to Prevent It From Happening To You
Refractory materials and lining reliability are critical factors for optimizing production yield and minimizing energy costs. Refractory failure can cause costly delays, increased energy expenses, or in some cases, complete shutdown while repairs are made.
The more you know about common refractory failures, the better you can avoid them.
Click To Tweet
Why Refractories Fail
Refractory failure is a major cause of production delays as well as a major contributor to plant outages. Understanding why a refractory material fails requires a thorough analysis of many related factors.
Castable Cracks
Much like cement mix, castable linings are not in a finished state when they leave a manufacturing facility. This means that the final product is dependent upon proper installation.
Materials must be mixed with clean water within the right temperature range and installed and cured before water is removed during the dry-out. If dry-out is not done in a slow and controlled manner, shrinkage may occur. Some shrinkage and cracking is normal, but if it becomes excessive, it could be a consequence of poor installation using too much water.
Roof Collapse
- Fiber modules: If the modules and support anchoring are missing, the most likely cause is faulty installation or corrosion caused by sulfur or rust. If the support anchoring is intact, it is more likely a result of mechanical abuse. Make sure you check the fiber to see if it was torn off the anchoring or has signs of water damage. It is always important to look at the area affected and take note of what it is telling you.
- Older refractory ceilings were lined with firebrick, which is heavy and prone to collapse. If not totally collapsed, they may crack due to thermal stress. An experienced refractory brick mason can repair this issue, but you may opt for an easier to apply material, such as castable or fiber modules.
Leaning Walls
It’s not all that uncommon to see inner walls lean slightly. However, dramatic leaning could signal that the floor isn’t level, which can cause failure. A lot of wall issues are also due to inadequate expansion provisions, such as increasing operating temperatures to higher than expected. The key to making the best selection is investigating both the ambient and hot strength properties.
Mixing Materials
While it’s not uncommon to mix refractory materials , particularly around openings such as doors (fiber and brick), peep sights (IFB, castable, fiber modules) and burner blocks. Because dissimilar materials often have different chemical properties at elevated temperatures, this can result in vulnerabilities around those areas, which can lead to refractory failure. Avoid these issues by using similar refractory materials to those surrounding openings to create the best possible seal.
Focus on Reliability
Finding the root cause of a refractory failure must take into account factors such as material type, manufacture date, plant operations, material storage, mixing, installation, curing, and drying. By better understanding refractory materials and installation processes, you can help eliminate future failures. When it comes to refractories, don’t focus too much on cost, but on reliability. Remember that the best products and professionals for the job are typically not the cheapest.
Contact Us to discuss your refractory project and find out how we can help.
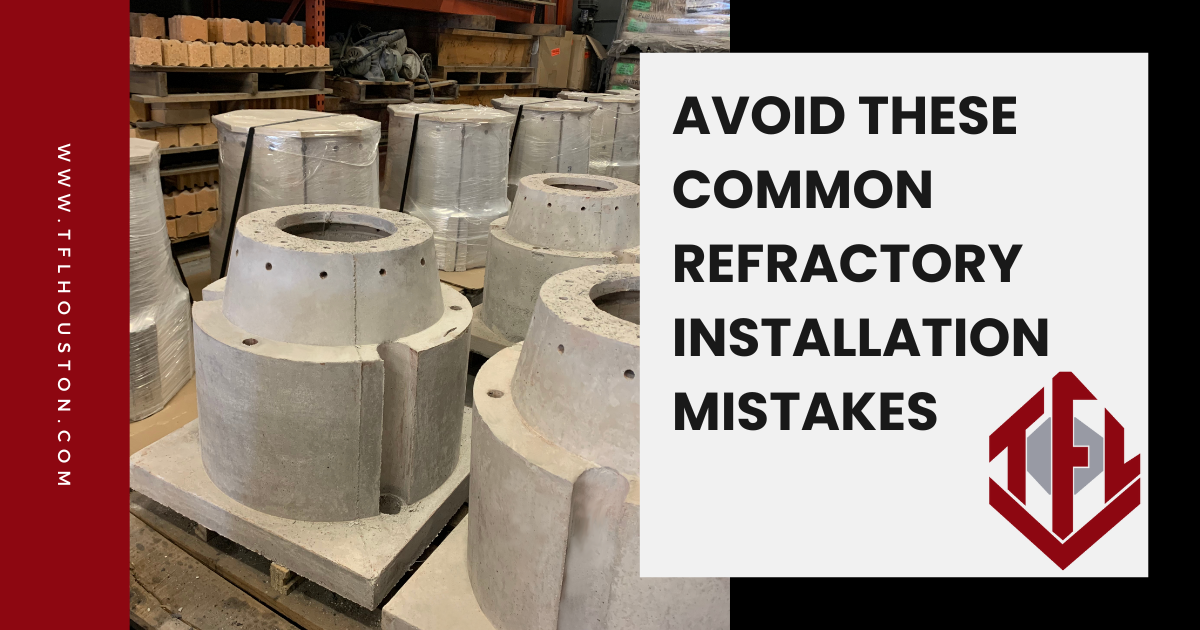
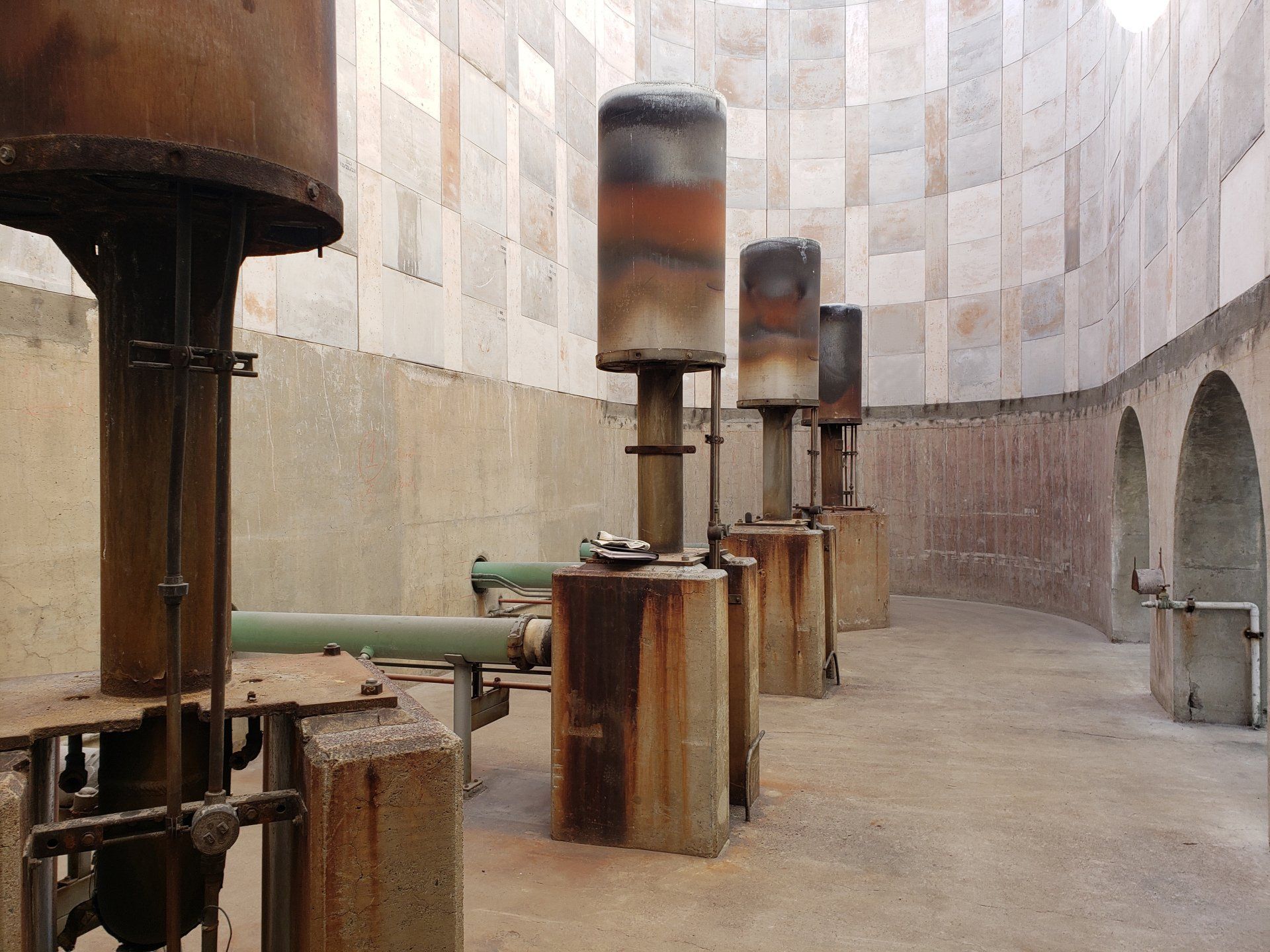
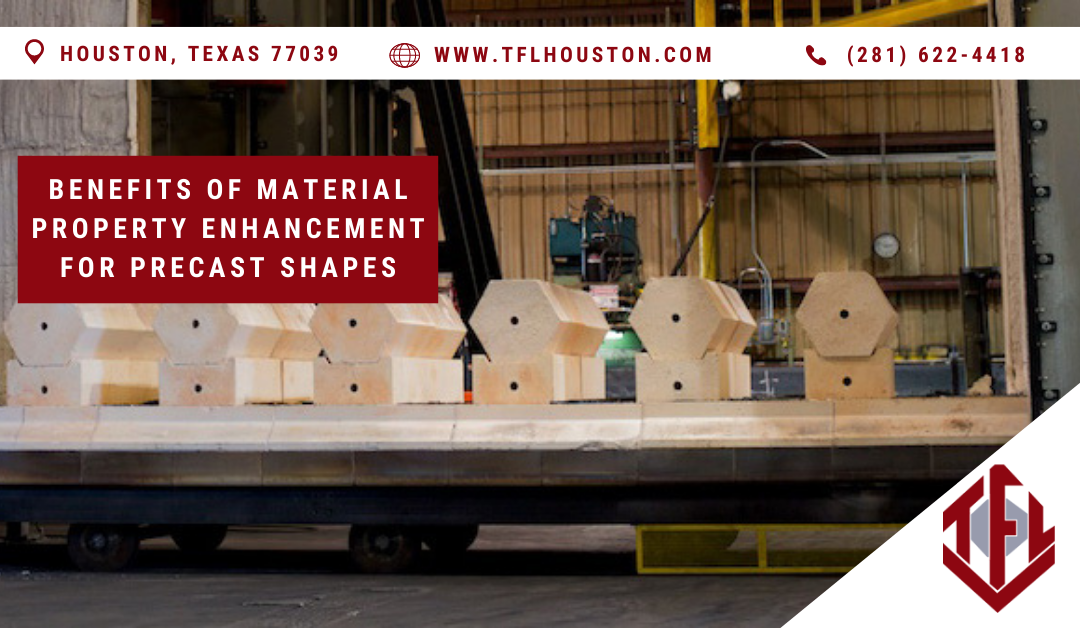
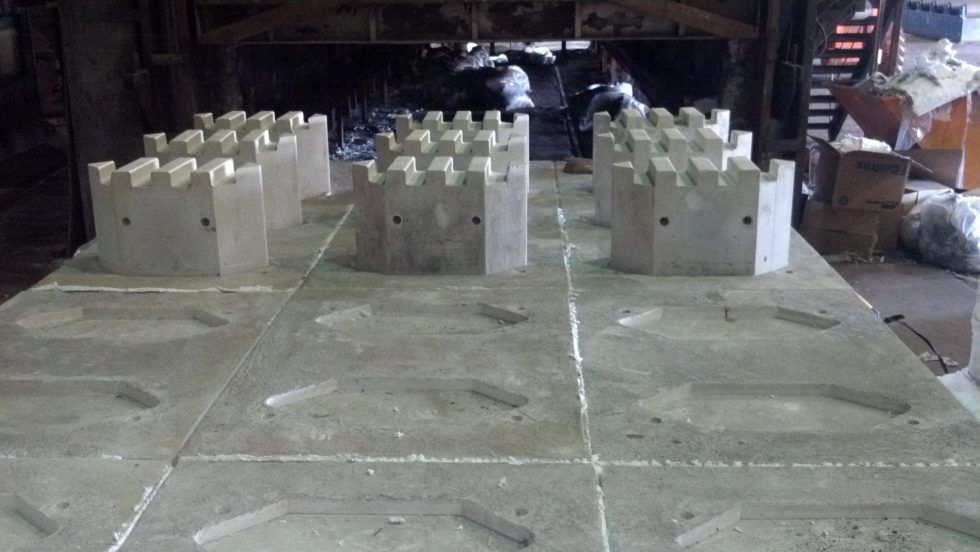
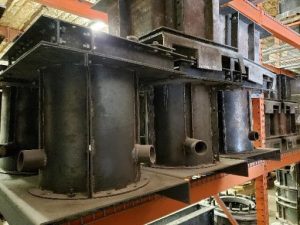
TFL Uses Custom Molding Techniques to Make Precast Refractory Shapes With Extremely Tight Tolerances
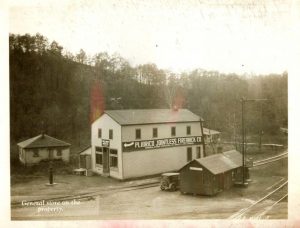